Китайський звичайлиті вироби з нержавіючої сталізгідно з кресленнями та вимогами.
Нержавіюча сталь має мінімальний вміст хрому 10,5%, що робить її більш стійкою до корозійних рідин і окислення. Він має високу корозійну стійкість і зносостійкість, забезпечує відмінну оброблюваність і добре відомий своїм естетичним виглядом. Литі виплавляні вироби з нержавіючої сталі «стійкі до корозії» при використанні в рідких середовищах і парах при температурі нижче 1200°F (650°C) і «термостійкі» при використанні вище цієї температури. Основними сплавними елементами будь-якої виплавленої продукції на основі нікелю або нержавіючої сталі є хром, нікель і молібден (або "молібден"). Ці три компоненти визначатимуть зернисту структуру та механічні властивості відливки, а також сприятимуть її здатності протистояти нагріванню, зносу та корозії.
Як правило, нержавіюча сталь повинна бути відлитапроцес точного литтяіз золем діоксиду кремнію як зв’язком. Виливки з кремнезему з нержавіючої сталі мають дуже точну поверхню та продуктивність.
Завдяки своїм унікальним фізичним властивостям виливки з нержавіючої сталі популярні в широкому діапазоні застосувань, особливо в суворих умовах. Загальні ринки литва з нержавіючої сталі включають нафту та газ, рідинну енергію, транспорт, гідравлічні системи, харчову промисловість, фурнітуру та замки, сільське господарство... тощо.
Лиття за виплавленими моделями (лиття за виплавленими моделями) — спосіб точного лиття складних деталей наближеної до чистої форми з використанням повторення воскових моделей. Лиття за виплавленим моделлю або віск – це процес формування металу, який зазвичай використовує восковий візерунок, оточений керамічною оболонкою, для виготовлення керамічної форми. Коли шкаралупа висихає, віск виплавляється, і залишається тільки форма. Потім формують ливарний компонент шляхом заливання розплавленого металу в керамічну форму.
Цей процес підходить для багаторазового виробництва компонентів чистої форми з різних металів і високоефективних сплавів. Незважаючи на те, що зазвичай використовується для невеликих відливок, цей процес використовувався для виробництва повних дверних рам для літаків, із сталевими відливками до 500 кг і алюмінієвими відливками до 50 кг. У порівнянні з іншими процесами лиття, такими як лиття під тиском або лиття в пісок, це може бути дорогим процесом. Однак компоненти, які можна виготовити за допомогою литва за виплавленими моделями, можуть включати складні контури, і в більшості випадків компоненти відливаються приблизно за чистою формою, тому після відливання потрібно незначно або зовсім не дороблятися.
У процесі лиття за моделлю депарафінізація та випікання оболонок також потребують уваги. Після формування воску, покриття, сушіння та інших процесів наступним кроком є депарафінізація та випікання оболонок. Депарафінізація полягає в нагріванні воску в оболонці форми за допомогою гарячої води або пари, щоб змусити віск витікати з оболонки форми.
▶ Матеріали для лиття за моделлю, процес лиття за виплавленим воском:
• Вуглецева сталь: AISI 1020 - AISI 1060, C30, C40, C45.
• Сталеві сплави: ZG20SiMn, ZG30SiMn, ZG30CrMo, ZG35CrMo, ZG35SiMn, ZG35CrMnSi, ZG40Mn, ZG40Cr, ZG42Cr, ZG42CrMo... тощо за запитом.
• Нержавіюча сталь: AISI 304, AISI 304L, AISI 316, AISI 316L, 1.4401, 1.4301, 1.4305, 1.4307, 1.4404, 1.4571 та інші марки нержавіючої сталі.
• Латунь, червона мідь, бронза або інші сплави на основі міді: ZCuZn39Pb3, ZCuZn39Pb2, ZCuZn38Mn2Pb2, ZCuZn40Pb2, ZCuZn16Si4
• Корозійно-стійка сталь, стійка до морської води, високотемпературна сталь, високоміцна сталь, дуплексна сталь.
• Інші матеріали відповідно до ваших унікальних вимог або відповідно до стандартів ASTM, SAE, AISI, ACI, DIN, EN, ISO та GB
▶ Можливості ливарного ливарного виробництва
• Максимальний розмір: 1000 мм × 800 мм × 500 мм
• Діапазон ваги: 0,5 кг - 100 кг
• Річна потужність: 2000 тонн
• Сполучні матеріали для корпусного будівництва: золь кремнезему, рідке скло та їх суміші.
• Допуски: за запитом.
▶ Основна виробнича процедура
• Шаблони та дизайн інструментів → Виготовлення металевих штампів → Вприскування воску → Збірка суспензії → Будівництво оболонки → Депарафінізація → Аналіз хімічного складу → Плавлення та заливка → Очищення, шліфування та дробеструйна обробка → Постобробка або пакування для відправлення
▶ Процес після лиття
• Зняття задирок і очищення
• Дробеструйна обробка / піскоструминна обробка
• Термічна обробка: нормалізація, загартування, відпуск, цементація, азотування
• Обробка поверхні: пасивація, анодування, гальванічне покриття, гаряче цинкування, цинкування, нікелювання, полірування, електрополірування, фарбування, GeoMet, Zintec.
• Механічна обробка: токарна, фрезерна, токарна, свердління, хонінгування, шліфування.
▶ Переваги компонентів лиття по моделлю:
• Чудова гладка поверхня
• Жорсткі допуски на розміри.
• Складні та складні форми з гнучкістю дизайну
• Можливість відливати тонкі стінки, отже легший ливарний компонент
• Широкий вибір литих металів і сплавів (чорних і кольорових)
• У конструкції форм не потрібна тяга.
• Зменшення потреби у вторинній механічній обробці.
• Низькі матеріальні відходи.
▶ Чому ви обираєте RMC для індивідуальних деталей лиття за виплавленим воском?
• Повне рішення від одного постачальника від індивідуального дизайну шаблону до готових виливків і вторинних процесів, включаючи обробку з ЧПУ, термічну обробку та обробку поверхні.
• Пропозиції щодо зниження вартості від наших професійних інженерів на основі ваших унікальних вимог.
• Короткий термін виготовлення прототипу, пробне лиття та будь-які можливі технічні вдосконалення.
• Скріплені матеріали: Silica Col, рідке скло та їх суміші.
• Гнучкість виробництва від малих до масових замовлень.
• Сильні виробничі можливості аутсорсингу.
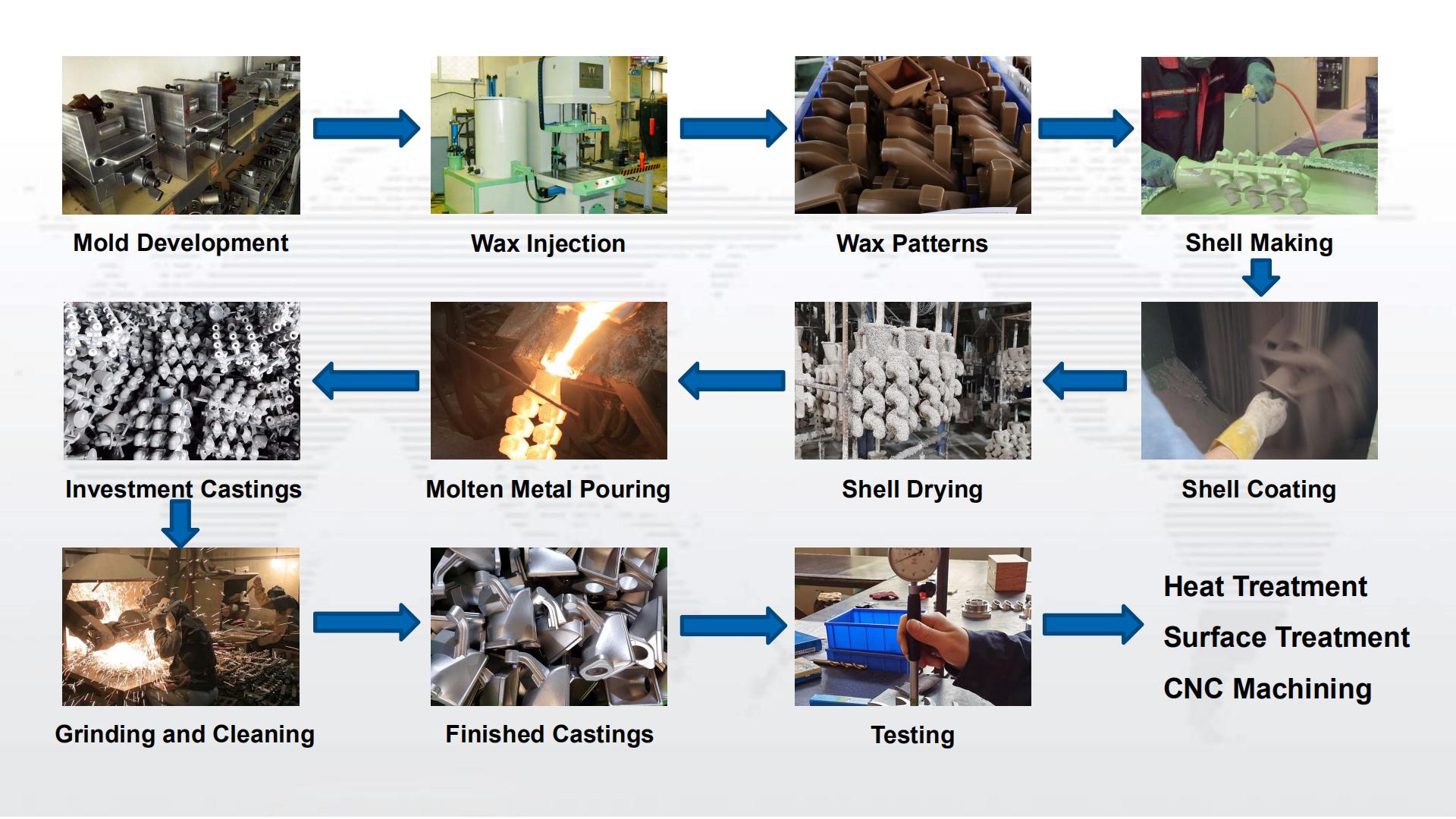
-
Лиття з сірого чавуну на замовлення
-
Обробні деталі з ЧПУ з ковкого чавуну
-
Лиття по виплавлюваним моделям із ковкого чавуну
-
Виливки з ковкого чавуну, покриті смолою
-
Деталі для піщаного лиття з ковкого чавуну
-
Виливки з піску з ковкого чавуну
-
Нестандартне лиття з нержавіючої сталі
-
Дуплексна нержавіюча сталь 2205 / 2507 Інвестиційна...
-
Дуплексне лиття з нержавіючої сталі
-
Виріб з нержавіючої сталі, литий за втраченим воском
-
Лиття з нержавіючої сталі, що зміцнюється дисперсійним процесом
-
Нержавіюча сталь 304/CF8 Лиття по моделлю